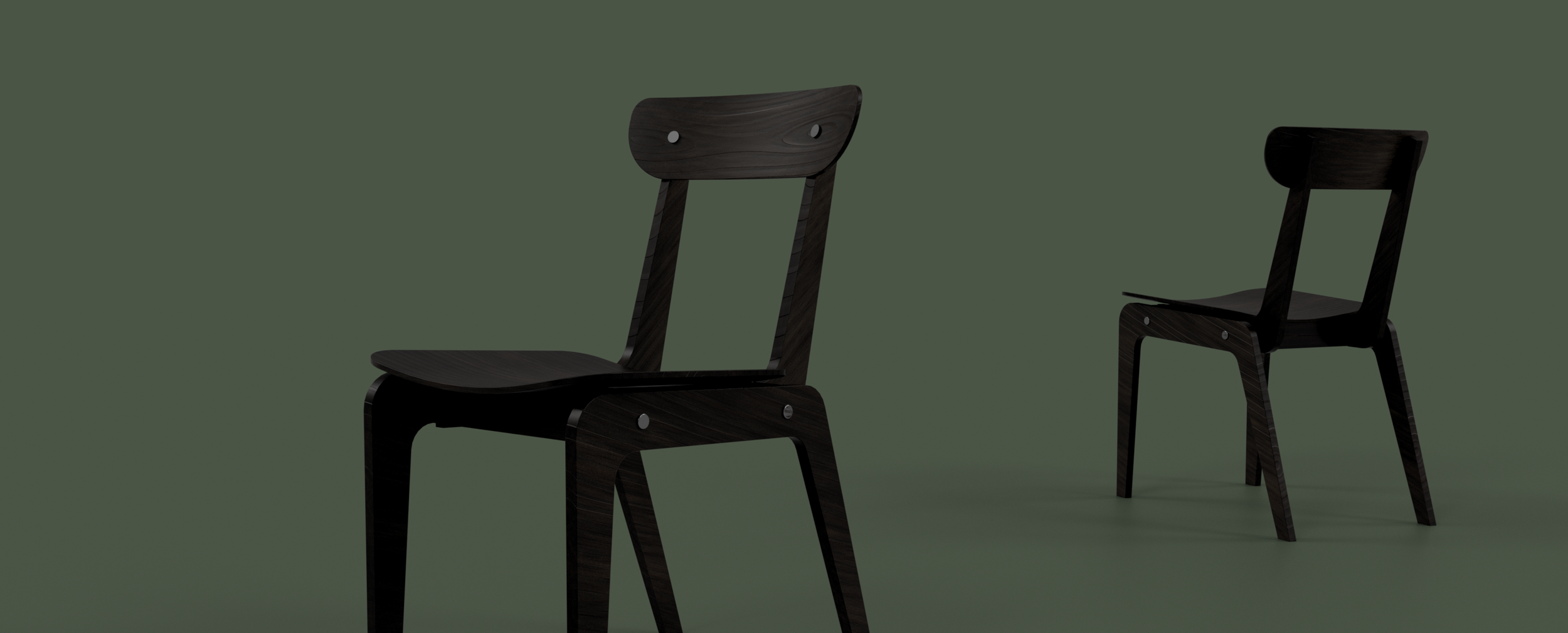
alma, designed during a semester in Copenhagen, explores the intersection of Scandinavian reduction and practicality. made entirely from birch plywood and a few pieces of hardware, the chair is designed to be flat-packed and easily disassembled, emphasizing sustainability, efficiency in production, and ease of transport.
IDEATION
focused on reduction and the use of negative space—distilling the form to its essential elements while exploring how openings and voids could create visual lightness and structural clarity.
FABRICATION PROCESS
SKETCHING + QUICK MODELING
The sketching phase centered on the principle of reduction—stripping the form down to its most essential components while maintaining a sense of strength and elegance. Early explorations played with the use of negative space, using cutouts and subtle voids to invite light through the form and create visual contrast through shadow. This approach allowed the chair to feel both structural and grounded, yet open and airy, balancing aesthetic appeal with functional clarity. Each line and surface was considered not just for what it added, but for what it allowed to remain absent.
TRADTIONAL WOOD WORKING
The build process was intentionally hands-on, using minimal tools to stay closely connected to the material and form. Each component was cut from birch plywood and carefully refined through extensive sanding and hand work, ensuring precision in the joinery and a smooth, tactile finish. This slow, deliberate approach allowed for continuous adjustment and refinement—reinforcing the chair’s balance between structure and lightness, and deepening the sense of craftsmanship embedded in the final piece.
LEG FIXTURE
The joinery was crafted using a Japanese hand saw, allowing for precise, clean cuts that aligned seamlessly with the chair’s minimalist aesthetic. Careful attention was given to following a consistent 700 cm radius, which defined the subtle curve shared by both the seat and backrest. This gentle arc not only added ergonomic comfort but also informed the overall mold and fit of the components—ensuring that each piece interlocked with clarity and intention, without the need for additional hardware.
A WORKING PROTOTYPE
The final working prototype was fully constructed in Copenhagen, capturing the essence of the design through careful craftsmanship and attention to detail. Building on that foundation, a sister chair was developed as an exercise in further reduction—distilling the original concept into just four components. This iteration pushed the limits of simplicity and efficiency, while maintaining the core principles of structural integrity, visual lightness, and thoughtful joinery.